Christmas is upon us and the decorations are ramping up. This year I’ve put together a run of sparkling Christmas trees. They’ll be in the store soon and will be sold in groups of three as pictured.
Category: Shop Notes
Ramping up
Sometimes you just need a project that you are trying to avoid to get you to work. For me, that has been a bathroom wall cabinet that I’ve designed and tweaked over the course of the past eight or so months. I’ve gotten advice about the joinery layout. I’ve selected and milled lumber for the case. I’ve pretty much committed to the build. And there the case parts sit next to my workbench. I can’t seem to get around to starting to cut dovetails.
That isn’t to say that I haven’t been working. Avoiding the bathroom cabinet project has motivated me to work on ramping up production of stock for my shop.
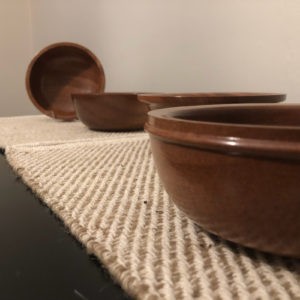
I have new bowls to add to the shop, including a gorgeous spalted sycamore bowl and several sapele bowls.
While figuring out joinery for the bathroom cabinet, I built a small wall-hanging tea cabinet for the kitchen.
I even got around to finishing a camp stool that I had started a few years ago.
I don’t look at this as procrastination. The bathroom cabinet is not a high priority. Even if it was a higher priority, the planned details of the cabinet demand that time be taken on each step. I’ll get to it eventually. But, as you may have already guessed, it has to be placed on the back burner again. A few days ago I started a new run of sliding lid boxes.
One of the biggest hurdles to being able to do a craft show is not having enough stock of what I want to sell. When going to a show, you need to have enough pieces for people to browse through and enough to replace anything sold on your shelves or tables. I also would like to have a range of price points for people; you can’t sell an $800 Roorkee chair to everyone. What that means is being able to do small production runs.
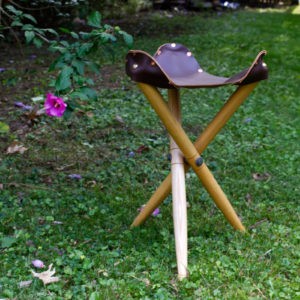
Before Christmas last year, at the request of a friend, I experimented with a production run of headphone clamps in solid walnut. I ended up making eight of these, based solely on the lumber availability in the shop. The design I settled on for the product, and the level of finish that I wanted, meant that I spent a substantial amount of time on each unit. While these weren’t a loss in the end (and a few are still for sale), they aren’t suited to a reasonable batch process.
My small run of sliding lid boxes this spring was another experiment in production work. In the end, these boxes proved to be a more than reasonable balance of time and enjoyment to make. I combined hand and machine work. I even gave the new laser engraver a chance to shine. The boxes were well received, with four given as gifts and one retained as a recipe card box. Still, they were an iterative design. The first test I did was a small mitered box. I settled on doing rabbeted ends for the run due to machine limitations; my current table saw is simply not up to the degree of precision needed for making mitered boxes.* This iteration was fine for the short run, but not preferable. The rabbeting layout resulted in relatively fragile corners where the lid is pulled out.
So, taking stock of what I have learned, I am preparing to do another, much more substantial, run of boxes. These will find their way to a shop near you sometime soon. These boxes will be mitered, and likely have keys added for extra strength. Mitered corners do place a bit of a delay on the run, as I plan on using the new table saw for these cuts. I plan on adding some color details to the ends. Fabric-covered bottoms are also a consideration. I will also be adding decorative engravings to the front and back of each box with the laser engraver. And, I should be doing a total of 48 of these boxes, a significantly higher output than I’ve done for anything to date. The run was initially going to have 24 boxes. However, I believe the lumber being used is stable enough to handle resawing, doubling the output (and work involved). That said, this is a good lesson in small-batch woodworking.
In addition to these boxes, I’m working on refining the design of my turned kalimbas. I’ve had a chance to see how seasonal wood movement affects the tuning. I’ve also gotten a better feel for the minimum size of one of these as currently designed. I hope to do a run of these for sale some time before Christmas.
I also have a few small gift items planned, all things that can be done as relatively quick batch production, and all things that should have a low price point.
The bathroom wall cabinet will just have to wait.
* I have been working on a Ridgid R4513 jobsite saw for more than five years. It has been a constant battle. The table is not flat. The miter slot are not properly machined. The fence constantly goes out of square. Forget about easily beveling the blade. Even the handle to raise and lower the blade is junk. Still, I’ve gotten a lot of work done with the saw. But times, they are a-changin’. I was ready to take the plunge on a Sawstop contractor saw. Unfortunately two things stopped me, and it wasn’t the price. You can only get the Biesemeyer-style fence with the 36 or 52 inch rails. Given my shop layout and size, I can’t reasonably fit the saw width-wise into the shop. I did think about the fact that I could cut down the rails to better fit the space. However, the Sawstop contractor saw’s motor is mounted off the back of the machine, taking up additional space. In a 9×16 foot shop, every inch counts.
I ended up settling on the Laguna Fusion F1. Space-wise, it won’t take up any more width than the Ridgid job site. It is a bit deeper, but not to the degree that I’d lose significant space in the middle of the shop. I had thought about the F2. This suffers from the same width issue as the Sawstop. I could certainly cut the rails down, and would feel less bad about modifying it, but there was also an issue with availability. The F2 is looking at a December ship date. The F1 is available now. Regardless, this will be a huge upgrade for the shop. I look forward to a flat table and blade that can actually bevel without going cattywampus.
The Long and Short of the Year So Far
I looked at my queue of posts to write today and realized that I’ve been slacking since March. That is about the long and short of the year so far. With the pandemic shutting things down in March, followed by what has to be one of the hottest summers I can recall, I haven’t had a chance to do much woodworking this year.
But Mousie, thou art no thy-lane,
To a Mouse – Robert Burns
In proving foresight may be vain:
The best laid schemes o’ Mice an’ Men
Gang aft agley,
An’ lea’e us nought but grief an’ pain,
For promis’d joy!
To say that this is a disappointment is an understatement. I had arranged to teach a class on kalimba making this summer. Unfortunately, that was cancelled due to the pandemic. The plan for the year was also to do at least one show. It appears most craft shows have been cancelled or are severely cut down. Add to that some of the other goings on since March and there is just no way I’ll have enough stock to do a show this year. That, of course, is no excuse for not getting what items I do have in stock photographed and up on the website for sale.
While I was able to travel to The Woodwright’s School in June for classes with Roy Underhill and Cara O’Connell, the whole experience was a bit surreal. Roy and Cara did a great job given the circumstances. Ed Lebetkin’s tool store, located above the school, was open to those of us in classes. This place is like a candy store for woodworking tools. I ended up leaving with a new rip panel saw, a 6 inch Starrett combination square, and a small incannel gouge. On the way down to Pittsboro, I stopped in Thurmond, WV, a ghost town in the bottom of the New River Gorge. The thing is, most of the places I drove through felt a bit like Thurmond – eery and abandoned. I stayed at the Celebrity Dairy, bed & breakfast and working goat farm, located between Siler City and Pittsboro. Fleming and Brit were wonderful hosts.
Main Street, Thurmond, WV The Inn at Celebrity Dairy Metal sculpture and other art can be found throughout the grounds. Looking toward the duck pond. Interesting pattern in the building The Woodwright’s School Inside the bench room Ed’s Tool Store
As if the heat this summer weren’t enough to keep me out of the workshop, we also embarked on Operation Kitten Fixin’ in May/June. The feral colony in our back yard produced four kittens this year. The process of trapping them, getting them fixed, and in the case of three of the kittens, socializing them, took a lot of time (and I wasn’t even the person who was doing most of the work!). I’m happy to report that three of the four kittens are now in their forever homes. One of them was captured a bit too late for socialization. The adult cats (minus one who has an appointment coming up) in the colony have also been trapped and fixed. With luck, no more kittens for at least a few years.
Sootball Comet (Orange) and Bernie
I have been able to build a few small projects on the lathe, including some coasters, a ring box, and a small vase. I haven’t taken photos of the coasters as I never applied finish to them. They are doing duty right now, but they really should have received a coat some sort of finish. I have some ideas for doing sets of these, including adding colored resin, but that’ll wait for another day.
The ring box was made during a period of shop cleaning and organizing. I’d started on the box at some point at least a year ago and never completed it. I’m still in the process of figuring out the best way to handle the interior foam/ring holding.
The vase was a bit of an experiment. I had a free day where the temperature in the shop wasn’t atrocious. I also had a scrap offcut of some ash that I had glued up (I can’t recall the original piece). It was a nice enough first go at the form. I painted the base with an oil paint mixed with boiled linseed oil. Danish oil was used for the top finish. The phrase “watching paint dry” clearly refers to oil, not modern latex, paint. Either way, it turned out well and is currently living on our front porch.
After my return from Pittsboro, and having taken a class on Slyod and green woodworking, I was inspired to build a shaving horse. This based on plans I found from Peter Follansbee, though I used only three legs instead of four.
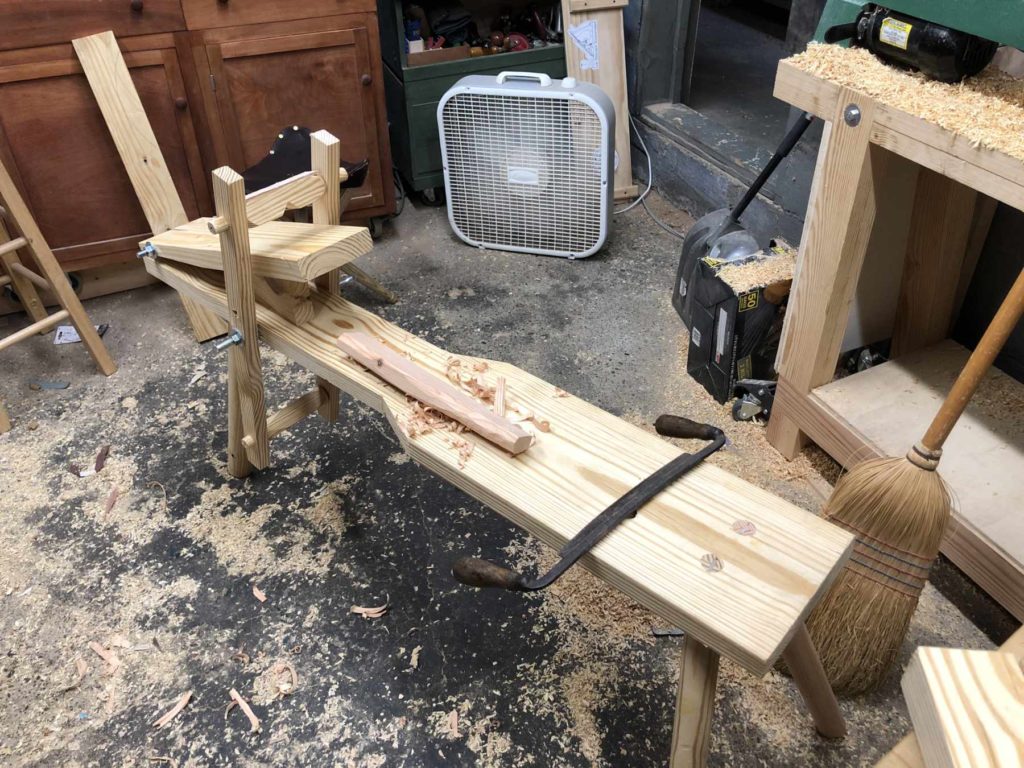
In addition, I designed and build a seiza bench. The bench is about 7 inches off the ground and angled forward slightly. The bench is made from beech with sapele wedges, finished with black wax and danish oil. The seat is an oblong octagon, with an underbevel to reduce its visual weight. The legs are set into shallow mortises that house the full width of the leg. Each leg is further secured with double-wedged double tenons. The shaping of the seat, as well as adjustments to the angle of the legs was a fun exercise. I have some beech left over and may make a small table to match.
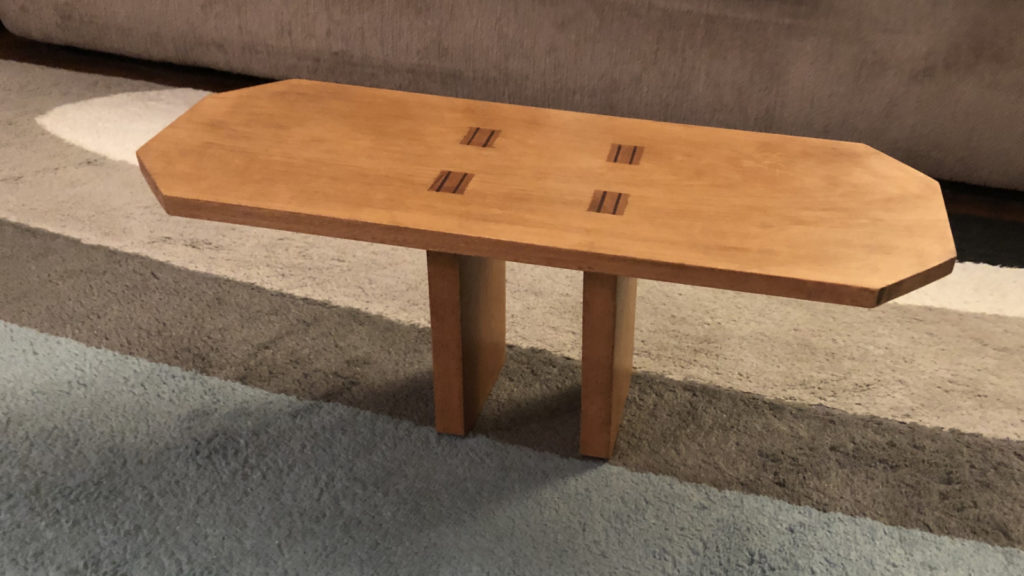
So that’s about the long and short of Wave I of the 2020 pandemic. With luck, the fall and winter will be much more productive and much less devastating for the world.
Matching Color (and Other Fun)
I recently took on a project involving the building of a dining table insert. The fabrication part of this table was fairly straight forward. The client provided me with their current table insert for reference during the build. The original insert is about 18 inches wide and 42 inches long. The ends had 40 degree bevels and cross-grain braces were screwed to the underside to prevent cupping.
After letting some 6/4 cherry acclimate to the shop, I started the process of milling it down to the 13/16 final thickness. I performed this milling over the course of about a week, re-flattening a face each day and taking a bit more material in an effort to allow the wood to full stabilize.
From there, it was just a matter of gluing up the strips of wood, taking extra care to ensure a good alignment of boards. (Patience is a virtue at this step. I went to fast on the first try and ended up with a center glue line that needed to be sawn apart and redone). Once the glue was hardened, I took the top back to the workbench and scraped off excess glue lines. The top was then trimmed to final width.
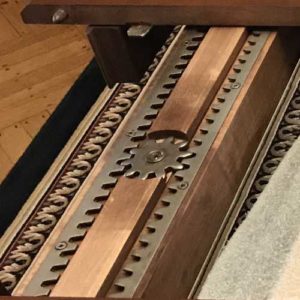
Trimming to final length was a bit more involved. If you haven’t seen or used a dining table that can extend, it’s worth understanding how the pieces all fit together. The most common mechanism for these tables is a gear-based slide. The slides are attached to the table base, and the two halves of the top are attached to the slides. When pulling the table from both ends, the top will pull apart allowing space for inserts to be added. How is everything aligned? With holes and pegs.
To make sure that everything would match up, I wanted to drill the locating holes in the edges before trimming the top to final length. I don’t usually write about woodworking products, but this one deserves mention. Milescraft makes a product called the JointMate.
The JointMate is a doweling jig that has a number of unique features. Like most doweling jigs, it has metal guide bushings to ensure a 90 degree hole. However, it can self-center on a board edge using four pins and rotating the jig, rather than having to use a screw-based system like other self-centering jigs. I didn’t need a self-centering mechanism for these holes. Instead, I needed to be able to use pre-existing holes to set the location on this new piece. To do that, the JointMate has both an adjustable fence and a pin alignment guide. You know you’re drilling in the right place because you’ve set the fence based on the original hole. You know you’re in line with the old holes because you slide the jig up to the old holes with the old and new piece clamped together. It’s an 11 dollar tool and is just brilliant to use.
With the peg holes drilled, I was able to put the tops together and mark the exact cuts for the length. Following trimmer, I then started the process of sanding the top to 320 grit. Slow passes up and down the boards ensured a nearly glass-like surface. The cross-braces were also sanded at this time. I also took the time to fabricate a piece of moulding that adorns the edges of the cross-braces.
The hardest part of making a piece to match someone’s existing furniture is the nature of wood and color. Unless you were the person who made the original piece, and saved documentation of your finishing and coloring regimen, it’s a trial and error process. Even if you can perfectly match a color today, the wood (particularly cherry) will darken over time, altering the color further.
I decided to attempt to match the current color as closely as possible. Rather than using a stain, which sits on top of the wood and hides the grain, I prefer to use water-based wood dye made by TransFast. I started by using a cherry dye that I had mixed awhile ago to give me some reference on the color. The existing top was much, much darker in color, necessitating mixing 5 additional samples of various coloring and darkness using the Dark Red Mahogany and Java dye powders. When colors appeared close, it was then necessary to start applying a topcoat to the sample boards to see how they would be affected by the wiping varnish. In the end, the color ended up being a near-dead match.
This is a cherry-dyed sample board. Much too light. What followed was a series of successive color samples. I tried different dyes in different strength levels. I then started to adjust the dye mixes to pull in the underlying red and brown. This piece of moulding was close, just a bit darker.
2019 Year in Review
This has been a busy year all around. The first half of the year ended up as mostly a wash. After hand surgery, I wasn’t able to get any substantial work done in the wood shop for several months. In that time, I was able to acquire lumber to prepare for several of the builds that were documented throughout the year.
The Great
These five projects took up much of the time in the work shop throughout the year. The Roorkee chair and trestle table, in particular, were multi-month builds from lumber acquisition to finish application. They were good exercises in wood selection and milling, as well as cutting joinery and processing large table tops. The bookcase and the plant stand were both furniture requests from family, allowing me to play with designs that I’ve seen elsewhere. I was also able to find two excellent sources of lumber going forward.
Any time I get to spend time at the lathe is a treat. Making kalimbas was a lot of fun. I’ve seen them made from boxes, flat boards, and gourds in the past. However, I haven’t seen any that were turned bowls. I plan on making several more of these in the next year, including playing around with segmented bowls to allow for larger resonating chambers.
The Good
I completed several projects that were not documented on the website. I was able to finish building out the workshop earlier this year, including adding lumber storage, building shop fixtures, building new shop storage, and setting up new cabinets. Lots of work was done clearing the yard of years of overgrowth. I also build a temporary solution for some of our rainwater management (I have plans for something much nicer next springtime). In addition, I spent a good amount of time helping out on a building renovation.
Other builds not documented on the site included cutting boards, pens, lamps, and a number of different experiments. You should see some of these for sale on the site in the next few months.
The Not-So-Great
Thankfully, this list is fairly short this year. I had a surgery on my right hand early in the year. That took me out of commission for a few months. I’m still dealing with residual weakness related to the carpal tunnel syndrome now, especially when using handled tools (Gent’s Saw, Shinto Rasp, etc). I’ll be having a second hand surgery in January 2020. Knowing what to expect should help the recovery process this time.
2020 Plans
I’ve spent a good amount of time planning for 2020 during the past month. There are several projects for the house that I hope to complete next year, including bathroom updates. This will mean building a new vanity, standing, and wall cabinets. I have a few furniture pieces that I’d like to build, including a Morris chair, more book cases, and some more lighting fixtures.
I will also be launching an online store for items that I build. Most of what will be available in the store will be small objects including boxes, cutting boards, pens, bowls, instruments, and some other functional and decorative items. As always, I also accept commissions. You can reach me on the contact page.
Happy New Year